包装フイルムのトラブル(包装作業編)
はじめに 前々号および前号では包装フイルム加工時におけるトラブルの例を示した。本号では包装時によく発生するトラブルについて原因と対策を考えてみる。すべてのトラブルについて述べることはできないので、基本的なものを中心に記した。また、対策についても、状況によって方法が異なるので100%解決するとは限らない。フイルム、加工条件、包装機、包装条件など、あらゆる要因を分析しなければならない。
包装作業時におけるトラブル ・横ピロー包装機でフイルムが蛇行する 原因としてはフイルムの厚薄、すべり性が良すぎる(悪すぎて蛇行する場合もある)などであるが、包装機に原因があることも考えられるので、包装機のローラーの平行度・回転異常、振動なども点検する必要がある。応急的には巻取を変えて様子をみる、ローラー上でフイルムが滑らないようにガイドをつける、フイルムのブレーキを強くする、パウダーが原因ならパウダーを拭き取る、逆にパウダーを散布するなどの対処が有効なこともある。根本的には包装フイルムの厚み精度を上げる必要がある。また、ラミネート条件、印刷デザインなども影響するので、まず現象をよく見て確かな原因を把握することである。
表1.フイルム蛇行の原因 | |
フイルム蛇行の原因 | 対策 |
フイルムに厚薄がある | ・包装機のローラーにガイドを付ける ・巻取のブレーキを強くする ・巻取を替えてみる |
フイルムが滑りすぎる | ・包装機にガイドを付ける ・ローラーに滑り止めのテープを巻く |
フイルムのすべりが悪い | ・パウダーを散布する |
印刷がかたよっている | ・巻の硬さを調節する |
包装機のローラー取り付けまたは回転がひずんでいる | ・包装機のローラーを調整する |
ラミネートフイルムではPEまたはCPPがシーラントとして使用されているが、これらでもシール温度が異なる多くの種類がある。一定条件で包装するためには全く同じグレードを指定する必要がある。シーラントの種類が違うとシール条件も変化する。一般にはPE系よりもPP系のほうが高い温度を必要とする。基本的なミスもある。構成や貼り面、シール面を間違えたという例である。パウダーやシリコンなど、シールを阻害する物質で汚染されているとシールできない。また、PEやPPの処理抜けもシール性は低下する。OPP共押のような単体フイルムでもメーカーの違いによってシール条件が異なる。この問題については、原因さえわかれば対策は簡単である。
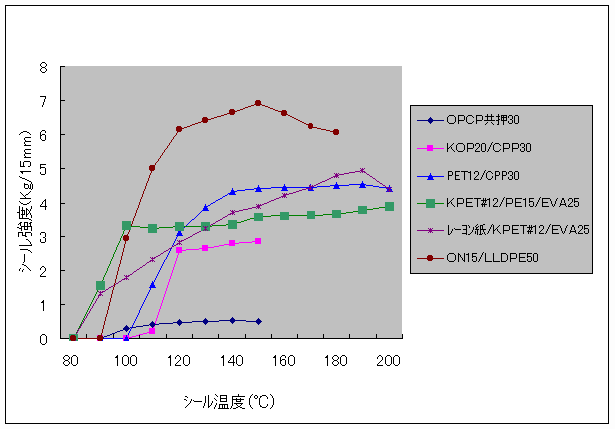
図1.各種フイルムのヒートシール適性 | |||||||||||||
シール温度℃ | 80 |
90 | 100 | 110 | 120 | 130 | 140 | 150 | 160 | 170 | 180 | 190 | 200 |
OPCP共押30 | 0 | 0 | 0.28 | 0.41 | 0.46 | 0.51 | 0.54 | 0.5 | |||||
KOP20/CPP30 | 0 | 0 | 0 | 0.21 | 2.58 | 2.65 | 2.78 | 2.84 | |||||
PET12/CPP30 | 0 | 0 | 0 | 1.58 | 3.11 | 3.88 | 4.33 | 4.42 | 4.44 | 4.44 | 4.5 | 4.54 | 4.43 |
KPET#12/PE15/EVA25 | 0 | 1.54 | 3.3 | 3.23 | 3.28 | 3.27 | 3.34 | 3.57 | 3.59 | 3.64 | 3.65 | 3.78 | 3.91 |
レーヨン紙/KPET#12/EVA25 | 0 | 1.33 | 1.78 | 2.32 | 2.81 | 3.23 | 3.71 | 3.89 | 4.21 | 4.45 | 4.8 | 4.96 | 4.4 |
ON15/LLDPE50 | 0 | 0 | 2.93 | 5 | 6.15 | 6.42 | 6.65 | 6.91 | 6.62 | 6.25 | 6.06 |
上記のグラフは各種フイルムのヒートシール適性を表しており、低温でヒートシールができるフイルムかどうか、シール強度は大きいかなどが読みとれる。例えばON/LLDPEはシール強度が高い、KPET/EVAは低温ヒートシールが優れているなどが視覚的に理解できる。KOP/CPPは高温でないとシールできないし、適正なシール温度範囲が狭いことがわかる。OPCP共押出しフイルムはシール強度が低い。このように、ヒートシール曲線をつくることによって、そのフイルムがヒートシールしやすいかどうかがわかりやすい。
・横ピロー包装機で内容物を噛み込んでしまう 横ピローではフイルムの背中シールを先にして筒状の中に内容物を定位置に並べていく。内容物とフイルムの接触面積が小さい場合、運転開始、停止、機械の振動などで内容物が移動し、内容物の上でシールしたり、カットすることがある。対策はいろいろあるが、すべり性の良くないシーラント(例:スリップ剤を添加していない蒸着用のCPPやPE)を使用して解決した例もある。
・横ピロー包装機できれいにシールができない OPPベースのフイルムは適性温度範囲が狭く、収縮しやすい。ベースフイルムがPETやONの場合は収縮しにくい。それだけきれいにシールできる。
OPPでも、低温シール性のシーラントと組み合わせ、表フイルムとシーラントの温度差を大きくするときれいにシールできるようになる。包装スピードを落としてシール温度を下げる、シールバーの汚れをとるなどの対策が有効なこともある。 (ベースフイルム)
PET-耐熱性があるのできれいにシールできる。
ON -PETほどではないが耐熱性がある。
OPP-PETやONに比べて収縮しやすいのでシール部が波打ちしやすい。 (シーラント)
CPP-レトルトに使用できるくらい耐熱性があるので低温でシールしにくい。PETやONならきれいなシールができる。OPP/CPPはシールが波打つ。
PE系-低温シールのアイオノマー樹脂、EMAA,EAAならきれいにシールできる。
一般のLLDPEでもCPP比べればシールはしやすい。低温シール性のLLDPE、コンテントの高いEVAも有効である。
・横ピロー包装機で完全密封シールができない 回転式シールの場合はシール時間が短いので、機械が新しい、フイルムが非常に低温でシールできるなどの条件以外では、完全密封シールは困難である。完全密封シールが条件ならボックスモーションタイプの包装機が条件となる。フイルムはベースが耐熱性、シーラントが低温シール性で、両者の温度差が大きいほど完全密封シールは楽になる。
・横ピロー包装機でもっとスピードアップをしたい シーラントフイルムのシール温度が低いほどスピードアップが可能となる。超低温シール性メタロセンPE、アイオノマー樹脂、EMAA、EAAなどを使用すると改善が期待できる。一方、耐熱PEやCPPは十分な温度と時間を必要とするので、スピードアップしにくい。
・横ピロー包装機でフイルムがカットされず連なってで てくる OPP、セロハン等では問題ないが、PETがベースフイルムの場合、包装機によってはカットできず、つながってでてくる場合がある。かなり古い包装機ではよく見られた光景である。最近の機械ではカッターの調整・取り替えで直ることが多い。ドライラミネートの硬化不足でも生じることがある。対策としては、機械のカッターを調整するか新しいものに取り替える、ドライラミネートのエージングを完全にするなどが有効である。それでも解決できない場合はフイルム構成を変更する必要がある。
・縦ピロー包装機でシールの底抜けを起こす 縦ピローでは底シール直後に内容物が上から落ちてくるので、シール部がまだ冷え切っていない状態で負荷がかかるため、シールが剥離することがある。応急的にはシール直後に冷風などで冷却すれば使用できることもあるが、基本的にはシーラントを溶融粘度の高いホットタック性に優れたもの、耐衝撃性に優れたものに変更する必要がある。
アイオノマー樹脂、EMAA、EAA、LLDPE(メタロセン樹脂も含む)はホットタック性に優れている。EVAは低温シール性樹脂であるが、ホットタック性はない。下図ではグラフが下にあるほどシール直後の加重による剥離が少なく、左にあるほど低温シーであることを示している。
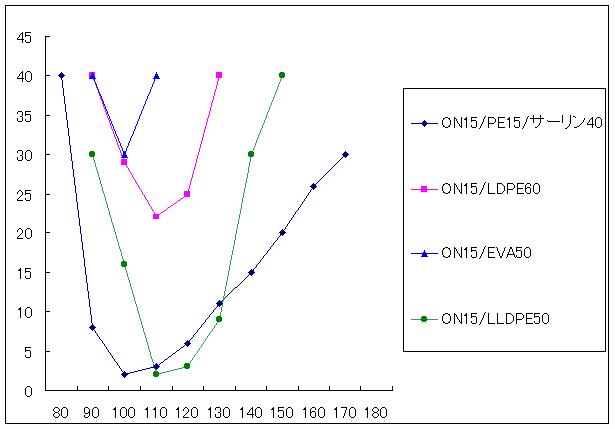
図3.各種シーラントのホットタック性
・縦ピロー包装機でピッチが合わない 横ピロー包装機でも同じであるが、光電管マークが正常に印刷されていない場合が考えられる。光電管マークの色が薄くないか、かすれていないか、印刷ピッチが一定しているかなどを確認する必要がある。また、フイルムのすべり性が悪いとスムースにフイルムが流れないのでピッチ不良になる。この場合はフイルムの表面のすべり性をよくする必要がある。すべり性のよい表基材への変更、スリップ剤の散布などが効果的である。
・縦ピロー包装機で表刷のインキがとれる 基本的には使用するインキの変更が必要である。グラビアインキの性質も用途に合わせていろいろあり、シールバーに触れても取れないような耐熱性、擦れても大丈夫な耐摩性、マット調のインキ、表刷か裏刷かわからないような光沢のあるインキ、光で退色しない耐光性など、用途によって使い分けられる。包装時にインキがとれる問題は、インキの耐熱性と耐摩性を向上させることによって防止できることが多い。どうしても解決できない場合は裏刷にする必要がある。
・縦ピロー包装機で白い粉がたまる 包装フイルムはすべり性を改善するためにデンプン系のパウダーを散布することがある。特に押出しポリコートでは必ずと言っていいほどパウダーが使用されている。縦ピローでは横ピローより擦れる部分が多いのでパウダーが取れやすい。たまったパウダーが袋内に落ちる可能性があるのでクレームとなる。パウダーの量を少なくする、包装機をこまめに掃除するなどの対策があるが、最近ではスリップ性の良いベースフイルムとノンパウダーのシーラントの組み合わせが効果的である。
・縦ピロー包装機でフイルムにシワが入る ホッパー部分ではフイルム表面がヘアピンのように擦れながらすすむ場所があり、ここでしわが入るときがある。表面のすべりが悪い時に発生しやすい。内面のすべりが悪いときにはシール部にしわが発生しやすい。柔らかくてすべりの良いフイルムがよい。
・給袋式充填機で、袋が複数枚連なり、うまく包装できない 袋に静電気がたまっている、シール部が波打っている、袋表面のすべり性が悪い、保管・輸送中に袋と袋の間の空気がなくなって、密着している、などの原因が考えられる。
対策として、包装機にセットするときに束をよくほぐし袋と袋の間に空気を入れる、袋の静電気を取り除く、すべり性を改善する、シールをきれいにするなどである。袋になってからの不具合では改善の手間が大変なので、包装設計の段階で対策を考える必要がある。
・給袋式充填機で、袋の口が破れる 一般的な給袋式包装機では、重ねられた袋の口を吸盤で1枚ずつ吸い取り、さらにもう一つの吸盤で袋の反対側からも吸着して口を広げる。圧縮エアを吹き込み、袋を膨らませてから内容物を充填後、シールする。この袋口を広げるとき、口またはシールが破れ、正常に充填できないことがある。原因としては、袋口の切り口がきれいにカットされていない(袋の切り口がギザギザまたはヒビ割れている)、シール強度が弱い、エッジ切れしやすいなどが考えられる。
・真空包装機でシール部にしわが入る
袋のシール時にしわが入るのは内面のすべり性が悪いときに多い。腰があってすべり性のよいフイルムではしわは入りにくい。袋の片面にたるみがある場合にもしわが入りやすい。
・縦ピロー包装機でピッチが合わない 横ピロー包装機でも同じであるが、自動包装機でピッチが狂うのは、巻取のピッチが一定していない、光電管マークが正常に印刷されていないなどが考えられる。印刷ピッチが一定しているか、光電管マークの色が薄くないか、かすれていないか、などを確認する必要がある。また、フイルムのすべり性が悪いとスムースにフイルムが流れないのでピッチ不良になる。この場合はフイルムの表面のすべり性をよくすることが必要である。すべり性のよい材質への変更やスリップ剤の散布などが効果的である。
一方、非常にすべり性が良いフイルムもあり、良すぎるためにピッチが合わない、横ズレするなどの問題が生ずることもある。
・縦ピロー包装機で表刷のインキがとれる 基本的には使用するインキの変更が必要である。グラビアインキの性質にもいろいろあり、シールバーに触れても取れないような耐熱性、擦れても大丈夫な耐摩性、マット調のインキ、表刷か裏刷かわからないくらい光沢のあるインキ、光で退色しない耐光性をもつインキなど、用途によって使い分けられている。包装時にインキがとれる問題は、インキの耐熱性と耐摩性を向上させることによって防止できることが多い。耐摩剤の添加、二液インキの使用も考えられる。
どうしても解決できない場合は裏印刷にしたり、印刷面をサンドイッチにする必要がある。同じインキでもフイルムによって接着性が異なるので、フイルムを変更することも考えられる。
・縦ピロー包装機で白い粉がたまる 包装フイルムはすべり性を改善するためにデンプン系のパウダーを散布することがある。特に押出しポリコートでは必ずと言っていいほどパウダーが使用されている。縦ピローでも横ピローでも擦れる部分が多いので、この部分でパウダーがたまりやすく、粒になって袋内に落ちる可能性もあることからクレームになる。
パウダーの量を少なくする、包装機をこまめに掃除するなどの対策が必要であるが、最近ではスリップ性の良いベースフイルムとノンパウダータイプのシーラントの組み合わせが効果的である。一般にPE系よりPP系シーラントのほうがすべり性はよい。
・縦ピロー包装機でフイルムに静電気が発生して粉末包装ができない ほとんどのプラスチックフイルムは静電気を帯びやすく、静電気による包装作業のトラブルは非常に多い。特に冬場の乾燥状態で湿度40%RH以下で要注意である。縦ピロー包装で顆粒、粉末が静電気によって舞い上がり、フイルムの内面にへばりついてきれいにシールができないという問題が最も多い。包装機をアースしてあっても、巻取を除電しても、トラブルの防止効果は低い。フイルムがフイルム同士あるいは包装機の部分と接触・剥離するだけで静電気が発生する。問題部分に直接、あるいは、直前に電離空気を吹き付けたり、導電性ブラシで擦ったりすれば、内容物や環境にもよるが、効果がでることもある。
プラスチックフイルムに静電気防止剤を練り込んだりコーティングした帯電防止フイルムを使用すれば効果は非常に大きい。OPP、PET、ON、CPP、LLDPEなどのフイルムに静電気防止タイプがあるが、特にOPPとCPPの帯電防止効果が大きい。少しの静電気であれば除電装置を付ける、湿度を上げる、内容物の水分や形状を工夫するなどが有効である。
・縦ピロー包装機でフイルムにシワが入る ホッパー部分ではフイルム表面がヘアピンのように擦れながらすすむ場所があり、ここでしわが入るときがある。機械の調整に問題がある場合も多いが、フイルムが原因の場合は、表面のすべりが悪い時に発生しやすい。内面のすべりが悪いときにはシール部にしわが発生しやすい。柔らかくてすべりの良いフイルムがよい。また、フイルムに厚薄がある場合にもしわが発生する。
・給袋式充填機で、袋が複数枚重なって給袋され、うまく包装できない 袋に静電気がたまっている、シール部が波打っている、袋表面のすべり性が悪い、保管・輸送中に袋と袋の間の空気がなくなって密着している、などの原因が考えられる。
対策として、袋の静電気を取り除く、シールをきれいにする、パウダーの散布などによってすべり性を改善する、包装機にセットするときに束をよくほぐし袋と袋の間に空気を入れる、などである。袋になってからの不具合では改善の手間が大変なので、包装設計の段階で対策を考える必要がある。シールをきれいにするためにはベースフイルムに耐熱性のあるPETを使用するのが有効である。
・給袋式充填機で、内容物が袋の底まで入らない 袋内面のすべり性が悪いと、内容物が袋の口付近で止まり、あふれてしまうことになる。液体では問題ないが、固形物、特にひねり包装などの個装品でうまく充填できないことがある。吹き込みエアーを強くして袋をいっぱいに広げてもだめな場合はフイルムの内面のすべりをよくする必要がある。
・給袋式充填機で、スタンドパックの底がうまく開かない 製袋時に型付けが強すぎるために、エアで袋を膨らませようとしても開かないことがある。機械的な問題もあるが、フイルムで改善するには底フイルムを耐熱性があり、柔らかくすることが有効なこともある。
・給袋式充填機で、袋の口が破れる 一般的な給袋式包装機では、重ねられた袋の口を吸盤で1枚ずつ吸い取り、さらにもう一つの吸盤で袋の反対側からも吸着して口を広げる。圧縮エアを吹き込み、袋を膨らませてから内容物を充填後、シールする。この袋口を広げるとき、口またはシールが破れ、正常に充填できないことがある。原因としては、袋口の切り口がきれいにカットされていない(袋の切り口がギザギザまたはヒビ割れている)、シール強度が弱い、エッジ切れしやすいなどが考えられる。 ・真空包装機で密封シールができない チャンバー式の真空包装機のシール方法はほとんどがインパルスシール方式の片面シールである。ガゼット袋の場合は二枚の部分と4枚の部分ができるので、完全密封性が問題になることがある。表面にPETなどの耐熱性に優れたフイルムを、シーラントでは低温シール性に優れたものを使用する必要がある。
・真空包装機でシール部にしわが入る 袋のシール時にしわが入るのは内面のすべり性が悪いときに多い。腰があってすべり性のよいフイルムではしわは入りにくい。また、袋の片面にたるみがある場合にもしわが入りやすい。どうしてもしわが入る場合は、応急処置として、シール時間を長くして温度でしわを押しつぶして密封する、パウダーで内面のすべり性を良くするなどの方法がある。機械に押さえバーがついている場合はほとんど問題は生じない。
・深絞り真空包装機で深絞りがうまくいかない 原因は包装機の場合とフイルムの場合がある。一般的な絞り材としてはCN/CPPやCN/EVOH/CPP等がある。シーラントはPE系のものもよく使用されている。また、共押出しフイルムも絞り材として適性がよく、バリヤー性に優れたものも多い。適切な包装フイルムを使用してもうまくいかない場合は包装機に原因がある場合が多い。フイルム加熱温度、包装スピード、シール温度などを調節する必要がある。
・深絞り真空包装機で絞りが不均一になる フイルムの絞り適性が良くない、包装時の加熱温度が低い、加熱ムラがある、真空状態がよくないなどの原因で、絞りが不均一になり、のびた部分とのびが悪い部分にハッキリとした境目ができることがある。このような現象をケロイドができるなどと表現する。特にPP系のものに生じやすい。対策としては加熱温度の調整もあるが、フイルムの選定が問題であることもある。一般に押出しや共押出しフイルムに比べてドライラミネートは不利であるが、のびのよい接着剤を使用することによって改善されることもある。
・深絞り真空包装機でラベルやシール部でカールが発生する スライスハムの真空包装などでラベル部分がピンと張っているのがよく見かけられる。しかし中には強くカールしている場合もある。
異種のフイルムを貼り合わせるとカールするのが当然であるが、貼り合わせ時の張力(引張テンション)やシール温度条件を調節することにより、ほとんどカールしない包装フイルムをつくることもできる。ただし、PET厚番手などの耐熱性をもつ材質を用いれば調節しやすい。
・カップシーラーでシールができない 完全密封する場合、カップがPPならフタ材のシーラントもPPでないと熱接着できない。PEならPE同士でないとシールできない。同じ系統の樹脂であることが条件になる。LLDPE,メタロセンPE、EVAなどはPE系としてシール可能である。イージーピールの場合はPEカップ用、PET用、PP用などがあり、カップの種類によってシーラントを選択する必要がある。また、ノンボイル、ボイル、レトルトなどの用途別グレードもあるので慎重な対応が要求される。結局は実包試験を実施するのが確実な方法である。
・カップシーラーでシール部にしわが入る フイルムが柔らかすぎる場合に引張りを強くするとしわが入りやすい。特にON系のフイルムでは吸湿すると腰がなくなるので、包装スピードを落とす、テンションをゆるくするなどが必要となる。
・コーヒーミルクなど、ポーションパック機でピッチが合わない 容量の小さいコーヒーミルクや一口ゼリーなどのポーションパックはPETをベースにした印刷フイルムがよく使用されている。PET/AL/シーラントやPET/VMPET/シーラントなどの構成である。容量が小さいがゆえに一つ一つのピッチが狭く、非常に厳しい精度が要求される。PETは耐熱性および強度に優れており、印刷やラミネートの加工によってピッチが狂いにくい。しかし、12μでは引張り具合によって伸縮が生じるので、PET16μを使用する場合もある。ヨーグルトはアルミベースが多く、カップゼリーの場合は比較的余裕のあるピッチなのでON系のラミネートフイルムがよく使用されている。
・イージーピールのカップでフイルムがピンと張らない PET構成では寸法安定性が良いので、ホット充填以外ではピンと張ることはない。ON系ではボイルによってONが収縮するので張ることになる。ただし、90℃以上のボイルが必要である。またONが乾燥しているときにはよく張り、吸湿するとゆるくなる。シール時のテンションの調整具合も影響する。
・ひねり包装機でフイルムが破れる ひねり包装ではMST(防湿セロハン)とOPE(一軸延伸ポリエチレン)が主流である。
MSTの場合は乾燥すると包装時に破れることがある。また、夏期のセロハンは保水剤が少ないので冬に使用すると破れやすい。
OPEの場合はたてひねり用、よこひねり用があり、包装機によって選択する。内容商品の形状によっても裂けやすいことがある。
・ひねり包装機で静電気が強すぎる ひねり用のフイルムとしては一軸延伸PE(OPE)および防湿セロハンが主流である。防湿セロハンは帯電することはないが、OPEは条件によって帯電がひどいときがある。帯電するとシュートで滞る、内容物が包装されていないカラフイルムが機械にからみつくなどの問題が生じる。静電気防止剤を塗布することが確実な防止対策となる。ただし、静電気防止剤を塗布するとすべり性が悪くなることもある。
・角折包装機できれいにシールできない 防湿セロハンは両面シール性を持っているが、温度を上げてもきれいに剥離(開封)できる。また熱で溶解することもないので温度管理は非常にやりやすい。
OPP系のシール性フイルムでは、片面シールの場合は接着強度が弱く、両面シールではきれいに剥離できない。また、収縮するので適正な温度範囲は狭い。
KPETは耐熱性もあるので機械適性はよいが片面シール性のPETはコート面/非コート面の接着になるので、シール強度は弱い。また、メーカーによっては角折包装に適さないKPETもある。
・角折包装機でカールして包装できない 角折包装ではヒートシール性OPPや防湿セロハンの単体で使用されることが多い。単体フイルムであれば大きなカールは起こりにくい。しかし、単体フイルムでは印刷が表刷になって、インキがとれることもあるし、高級感が表現できない。そこで2枚のフイルムを貼り合わせてインキをサンドイッチにし、しかも蒸着フイルムなども利用することもある。異種のフイルムをラミネートすればカールが発生しやすい。特に外面にカールした場合は不良率が非常に高くなる。設計段階での材質の検討、貼り合わせ時の張力の調整、紙複合の場合は水分調整が必要である。アルミ箔複合などではエンボス加工するとカールを少なくすることができる。
・包装後のレトルト時に袋が収縮したり、破裂したり、内面密着し たりする レトルト用途の袋は設計段階から使用状態を把握して、耐熱性、耐衝撃性、バリヤー性などを確保した構成を決定しなければならない。ベースフイルム、バリヤー材、シーラントなどのフイルムだけでなく、印刷インキ、ラミネート接着剤もレトルト温度に合わせて選択する。また、ラミネート後のエージング条件も品質に影響する。
・袋に日付印字ができない 賞味期限や内容量など、熱転写の印字機によって表示することも多いが、フイルムの種類によってはうまく印字できないことがある。特に静電気防止タイプのフイルムは印字適性が悪いことがある。テープの種類を替えたり、転写条件を調整する必要がある。トラブルをなくすためには、実際のフイルムを使用して、あらかじめ印字テストをして確認することが必要である。 以上、包装時に起こるトラブルについて述べたが、フイルムが原因の場合もあるが、包装設計や包装機械に問題があることも多いので、広い角度から総合的に分析して解決しなければならない。